When asked about being awarded Life Member status by the national American Society of Civil Engineers (ASCE), Prof. Mo Ehsani responds jokingly “That just means that I’m really old!”
With age comes experience, and Prof. Ehsani has plenty of that. As well as the aforementioned Life Member status, which he describes as “a surprise”. He is also a Fellow of the American Concrete Institute (ACI), the Centennial Professor Emeritus of Civil Engineering at the University of Arizona, a past director of the Arizona Chapter of ACI and he has served as President of the Structural Engineers Association of Arizona. He has received B.S., M.S., and Ph.D. degrees from the University of Michigan and his research findings have been published in numerous academic and industry publications, including those published by ACI, ASCE, the Earthquake Engineering Research Institute (EERI) and more.
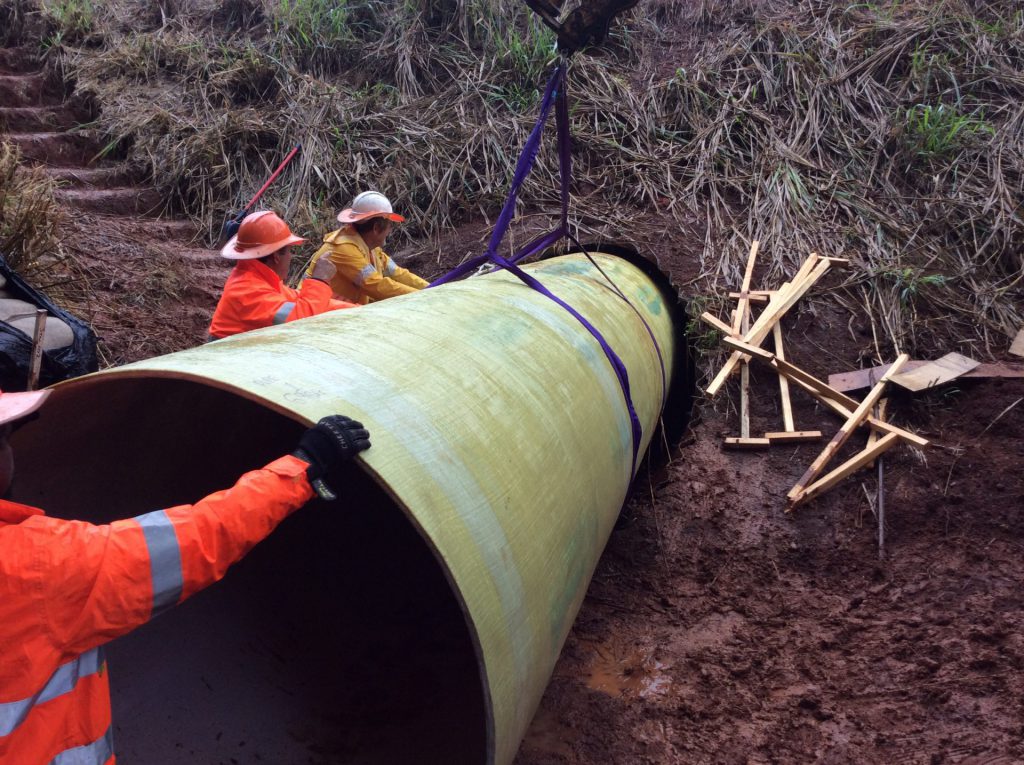
He has also been featured on CNN, National Public Radio, the History Channel, and in other media, including Engineering News Record (ENR) for his expertise on the strengthening of structures, particularly related to earthquakes, terrorist attacks and other potential structural disasters. 2019, the year Prof. Ehsani was awarded Life Member status by the ASCE, was also the year that the company he founded, QuakeWrap Inc., celebrated 25 years of infrastructure repair and renewal innovations.
“The sky is the limit” for the company according to Firat Sever, the manager of QuakeWrap’s Pipeline Division. “Where we are really growing are both in our Pipeline Division and in our Marine Division,” adds Prof. Ehsani, “because we have about twenty different patents in these areas so this is where we don’t have any competition and we really see great opportunity for growing the business”.
“Prof. Ehsani co-authored the first technical paper on using carbon fiber reinforced polymers for strengthening structures back in the 1980s.”
Incorporated in 1994, QuakeWrap has done pioneering work with Fiber Reinforced Polymer (FRP) and its applications for infrastructure repair and renewal innovations. “It was back in 1987 or so we had a crazy idea, one of my colleagues and I, to strengthen the infrastructure of buildings, bridges and pipelines and so on, and instead of using steel and concrete we would use carbon fiber” said Prof. Ehsani, “At that time it was a really crazy, novel idea so it took many years of testing and going to conferences and publications to convince the engineering community that this was ok”. He isn’t exaggerating about the novelty of the approach. In fact, Prof. Ehsani co-authored the first technical paper on using carbon fiber reinforced polymers for strengthening structures back in the 1980s.
It was the late 1990s before QuakeWrap really began to focus on working with, and reinforcing pipes. “We went to nuclear power plants where they have large diameter pipes as a part of their cooling systems. These are pipes that are anywhere from seven or eight feet to ten or twelve feet in diameter. And what happens with these pipes is that they usually have steel wires in them and over the years the wires start to corrode and the pipe becomes weak. So we were proposing that we could go inside these pipes and line them with carbon FRP”. Prof. Ehsani also came up with the idea of ‘Super Laminating’ pipes that were too small for maintenance workers to enter. The basic premise is that the FRP is placed around a “balloon-like device” called a Packer which is sent inside of smaller diameter pipes. Once the Packer has reached the point of the pipe that needs to be repaired or strengthened, the device can be inflated and the FRP will line the inside of that section of pipe. “It’s almost like a stent that they use in the medical field” he says.
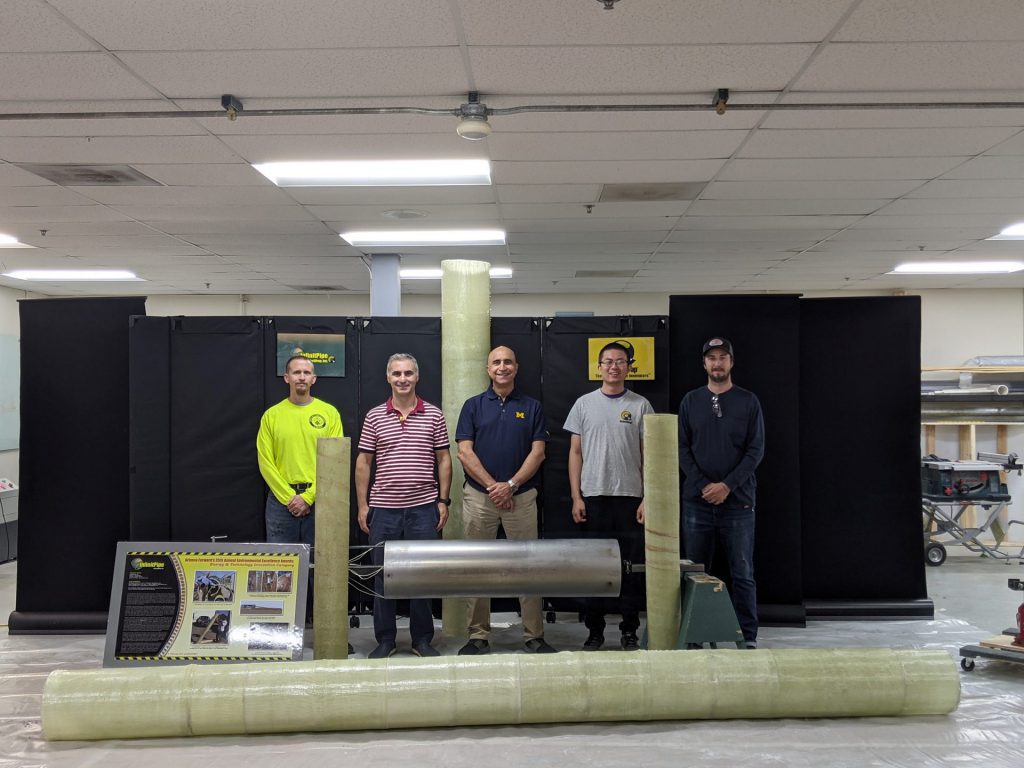
QuakeWrap recently received a grant from the United States Environmental Protection Agency (EPA) to further develop this technique to repair damaged water pipes without cutting trenches under roads and streets. They were also awarded a Phase II Small Business Innovation and Research (SBIR) grant ($1,000,000) by the US Department of Transportation (USDOT)/ Pipeline and Hazardous Materials Safety Administration (PHMSA) for development of an innovative oil and gas transmission pipeline repair system that can be installed without any excavation (no-dig). In addition to the potential to save lives and substantial amounts of money in pipeline integrity management, this new technology is also expected to reduce methane emissions from natural gas lines significantly by stopping and preventing leaks.
Environmental concerns often get a mention in Prof. Ehsani’s work. As well as avoiding environmental damage by super laminating pipes with FRP, QuakeWrap has also sought to improve environmental friendliness through its revolutionary StifPipe® and InfinitPipe® innovations. StifPipe® consists of a custom-designed sandwich structure without the need of excessive layers of carbon fiber. It is a high-strength, lightweight, and corrosion resistant product ideal for water, wastewater, stormwater, oil, gas, and other fluid conveyance systems subject to internal and external loads. StifPipe®’s strength to unit weight ratio is unmatched by any material used in the pipeline industry, according to Prof. Ehsani. It can be used for structural pipeline rehabilitation with trenchless technology (by the wet layup or sliplining method) or new pipe installation. Sliplining with StifPipe® typically does not require any jacking equipment due to its light weight.
“StifPipe®’s strength to unit weight ratio is unmatched by any material used in the pipeline industry.”
Another innovative technology by QuakeWrap is the InfinitPipe® system, which enables making essentially joint-free pipeline on-site. Most pipes manufactured to date require extensive heavy equipment to handle, and manufacturing in a large plant. These larger pipe sections are typically made in 5-10 meter pieces and are shipped to the job site for assembly in the field. These logistics add significant transportation and installation costs. Worse, the joints on these pipes are the weakest links, where water, gas or oil can leak and cause environmental damage. For sewer pipes, these joints become a source of penetration of roots and require a constant maintenance expense. InfinitPipe® overcomes all of these limitations. This innovative pipe takes advantage of long-recognized engineering principles of FRP, and uses these materials to make a pipeline on a mobile manufacturing unit (MMU) by producing approximately 10 ft of pipe every 30 minutes in the field, requiring no joints except for branch connections or bends greater than a certain limit depending on the pipe size and design. InfinitPipe®’s flexibility is comparable to plastic pipes and can accommodate FRP and plastic fittings for such connections.
Using this technology to avoid environmentally disastrous leaks for pipes carrying everything from water to oil to sewage is sure to become more and more popular as environmentalism gains momentum. The Keystone XL pipeline’s developer halted all construction on the project in June after its permit was revoked by the Biden administration. Environmentalists and Native American groups had fought against the project for more than a decade due to fears that a leak could do untold damage to local ecosystems and tribal lands. Innovations like StifPipe® and InfinitPipe® could help ease environmental concerns and ensure smoother business dealings for all involved. “In a couple of years, I anticipate that we will start getting a good share of that pipe repair market in the oil and gas industry upon finishing this grant project from the US Government” says Firat.
Looking to the future, Prof. Ehsani and QuakeWrap are eager to expand their pool of talent going forward to build on the success of the past. “Every year for the past seven years we have been offering twice a year a contractor certification and training course”. Helping to train engineers and installers to work with their technology is sure to improve QuakeWrap’s hold on the market in the coming years.