Industry is all about balance. Workload is managed by cost and labor. In turn, success is a causality of finding the right balance of all three. These metrics, however, only work when viewed through a purely fiscal lens. The world, its communities, and the needs of these people, are not figures and bottom lines. When we throw in the environmental component, the challenges become even greater still. What all this means is that the system of balancing cost against demand is an archaic one that is no longer fit for purpose. Other, less tangible considerations need to be taken into account too. Take housing for instance, the equation is far more complex than ‘build more houses.’ For many reasons, social, financial and environmental, this is simply not possible. However, housing is such a fundamental element of society that it simply cannot be overlooked. UN-Habitat estimates that 3 billion people (around 40 per cent of the world’s population) will need access to adequate housing by the year 2030. The organization is also clear on the vital need for a change in these numbers. “Access to housing is a precondition for access to employment, education, health, and social services. In order to address the current housing challenges, all levels of government should put housing at the center of urban policies by placing people and human rights at the forefront of urban sustainable development.” So, how do we remedy this? How do we rebalance the equation, factoring in these newer, more complex, considerations?
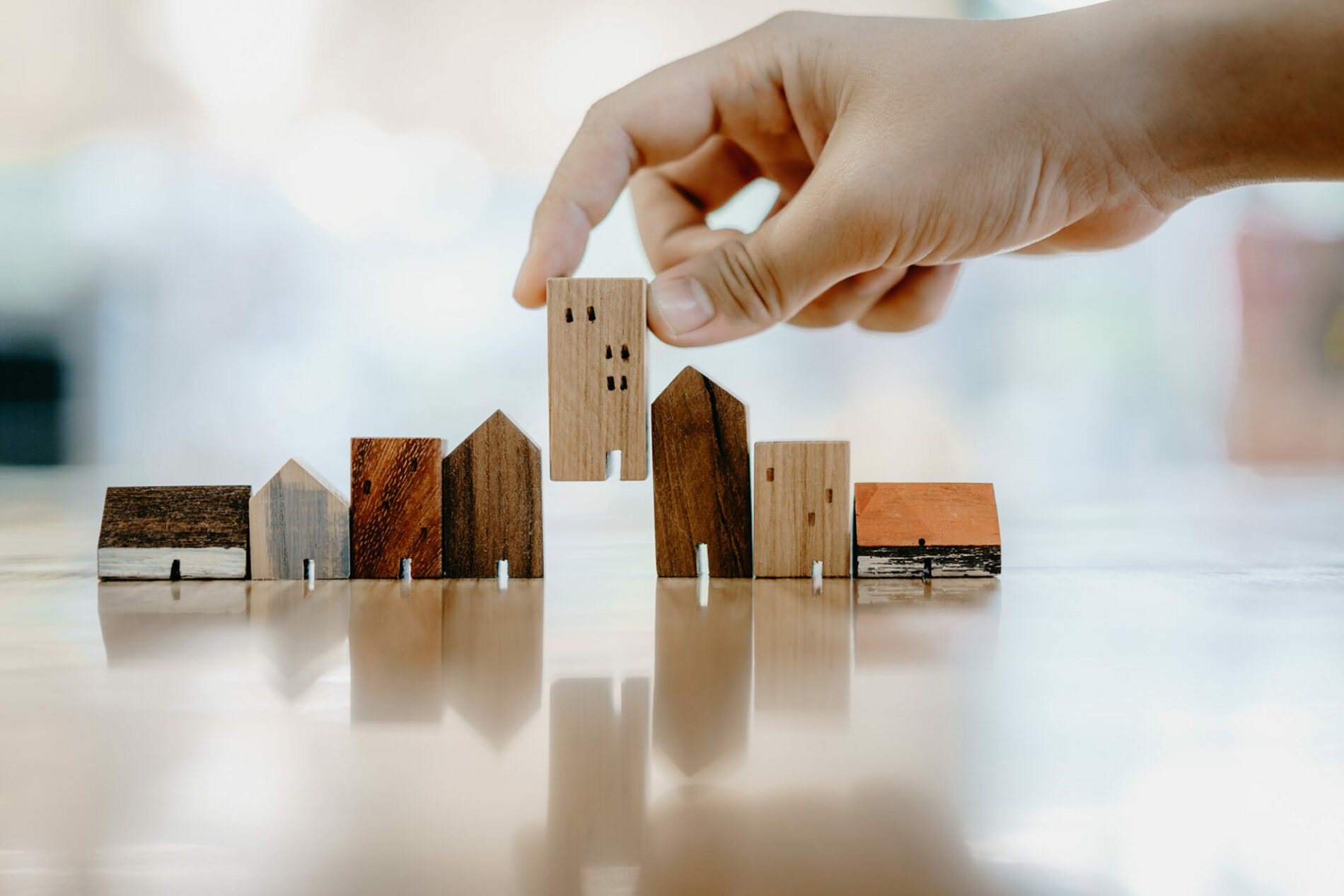
North America, and much of Europe too, finds itself in the midst of a housing crisis. Post-pandemic, communities are struggling to meet demands with an ever-growing list of factors that are vying for attention. Speed, cost, environmental considerations, not to mention the growing number of homeless people and families. It is an ever-growing challenge that seems to be getting worse, rather than better. This is where the question of balance comes in. Oftentimes, by using technology such as 3D printing to prioritize speed and cost, environmental elements are overlooked. Concrete, due to its cost and ease of use, becomes the go-to material. By addressing one issue, another rears its head.
In Maine, things are reaching a crisis point. MaineHousing has estimated that around 25,000 new housing units are currently needed to address the demand for homes. As costs climb to an all-time high and global events are displacing vast numbers of people, these figures are surely set to get worse before they improve. A recent report from MaineHousing is illuminating in this regard. “In 2022, the benchmark for measuring homelessness in Maine continued to be the annual Point-in-Time (PIT) Count, a federally required survey of sheltered and unsheltered persons experiencing homelessness on a single night in January. In 2021, (the first full year of the pandemic) there was a decline in the PIT due to no unsheltered count being done that year. In 2022, there was a dramatic increase from 1,097 in 2021 to 3,455 in 2022.”
“The truly remarkable element of this project is that the houses themselves will be 100 percent recyclable.”
One project in the state, however, is viewing the situation through a different lens. How could the individual elements of this crisis all be answered in tandem? Is there a way to combine fast, cost-effecting housing that is also environmentally sound? The answer, thankfully, is yes. The project is aiming to produce a community of 600-sq-ft, 3D-Printed, bio-based houses for those experiencing homelessness. The truly remarkable element of this project is that the houses themselves will be 100 percent recyclable.
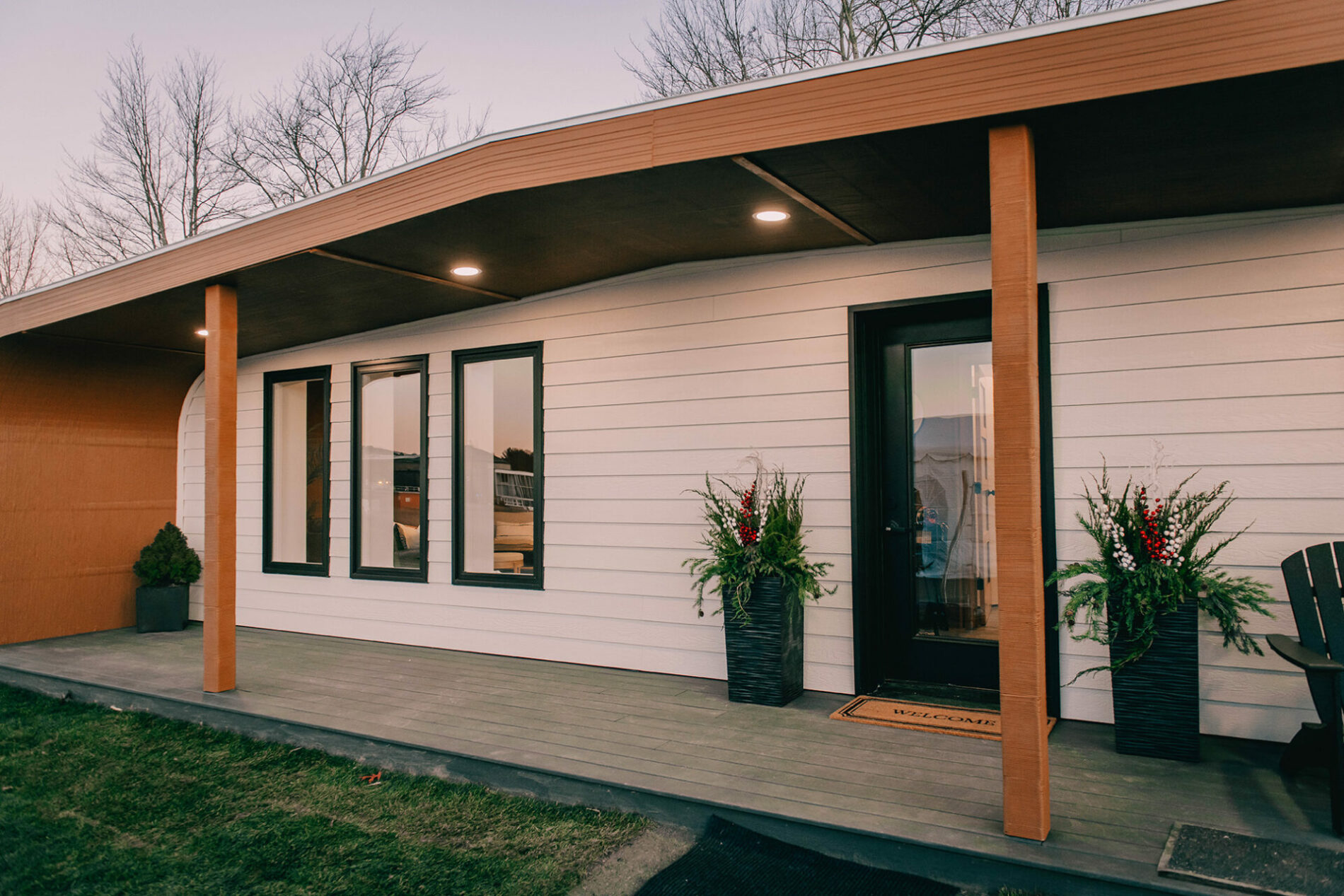
3D Housing has gathered a foothold in the construction industry due to its many benefits. It generates significantly less waste than traditional building methods while minimum space is needed to transport materials which brings down many factors such as energy, transportation and storage. In fact, such is the increase in its use, a recent report suggests that 3D printed construction will increase by an incredible 91% by the year 2028.
BioHome 3D is taking things even further. The company is producing the world’s first 3D-Printed house made entirely from bio-based, recyclable materials. As they explain, the method now allows for a simplified, cost effective and sustainable model of home design that is set to flourish. “Designed to address labor shortages and supply chain issues that are driving high costs and constricting the supply of affordable housing. Less time is required on-site building and fitting up the home due to the use of automated manufacturing and off-site production. Printing using abundant, renewable, locally sourced wood fiber feedstock reduces dependence on a constrained supply chain.”
The prototype was developed at the University of Maine Advanced Structures and Composites Centre (ASCC) through funding from the U.S. Dept. of Energy. Speaking about the innovation, Gov. Janey Mills said: “Our state is facing the perfect storm of a housing crisis and labor shortage, but the University of Maine is stepping up once again to show that we can address these serious challenges with trademark Maine ingenuity.” According to those at UMaine, the need for this development is the unquestionable damage that traditional construction methods are having on the environment. “The construction industry accounts for 39% of global carbon emissions. Sequestering 46 tons of carbon-dioxide for each 600-square-foot unit, BioHome3D stands as a pivotal solution for the construction industry. This technology addresses both operational and embodied carbon, and sets precedents for both sustainable construction material production and manufacturing.”
Photos by BioHome3D
The houses differ from other 3D printed methods in a number of ways. Each module is 100% additively manufactured with walls, floors and roofs all being 3D printed. The houses are insulated with wood fiber insulation and are 100% recyclable. According to Gov. Mills, the project is an example of highly creative thinking that will bring positive change to the people of Maine and beyond. “With its innovative BioHome3D, UMaine’s Advanced Structures and Composites Center is thinking creatively about how we can safely tackle our housing shortage, strengthen our forest products industry, and deliver people a safe place to live so that they can contribute to our economy.”
With the rise of 3D printing, it makes sense that the next step on this path is more sustainable practices in this regard. As the demand for sustainable building practices ramps up even further, we can expect to see much more of the BioHome 3D in the near future.