When it comes to modular, experience is what sets Axis Construction Corporation apart from its competitors. With projects that span the healthcare, commercial, educational, industrial, and retail sectors, Axis is a construction management and general contracting firm that can do it all. “I say this to clients all the time but the question they should be asking is not, ‘Can you do it?’ but ‘Have you done it?’” says John Buongiorno, Vice-President of the Modular Division at Axis Construction. As Buongiorno shares, the company takes immense pride in the array of projects it has in its impressive portfolio of work. These projects range from small-scale guard homes to multi-story healthcare facilities, all executed over an impressive 30 years in business.
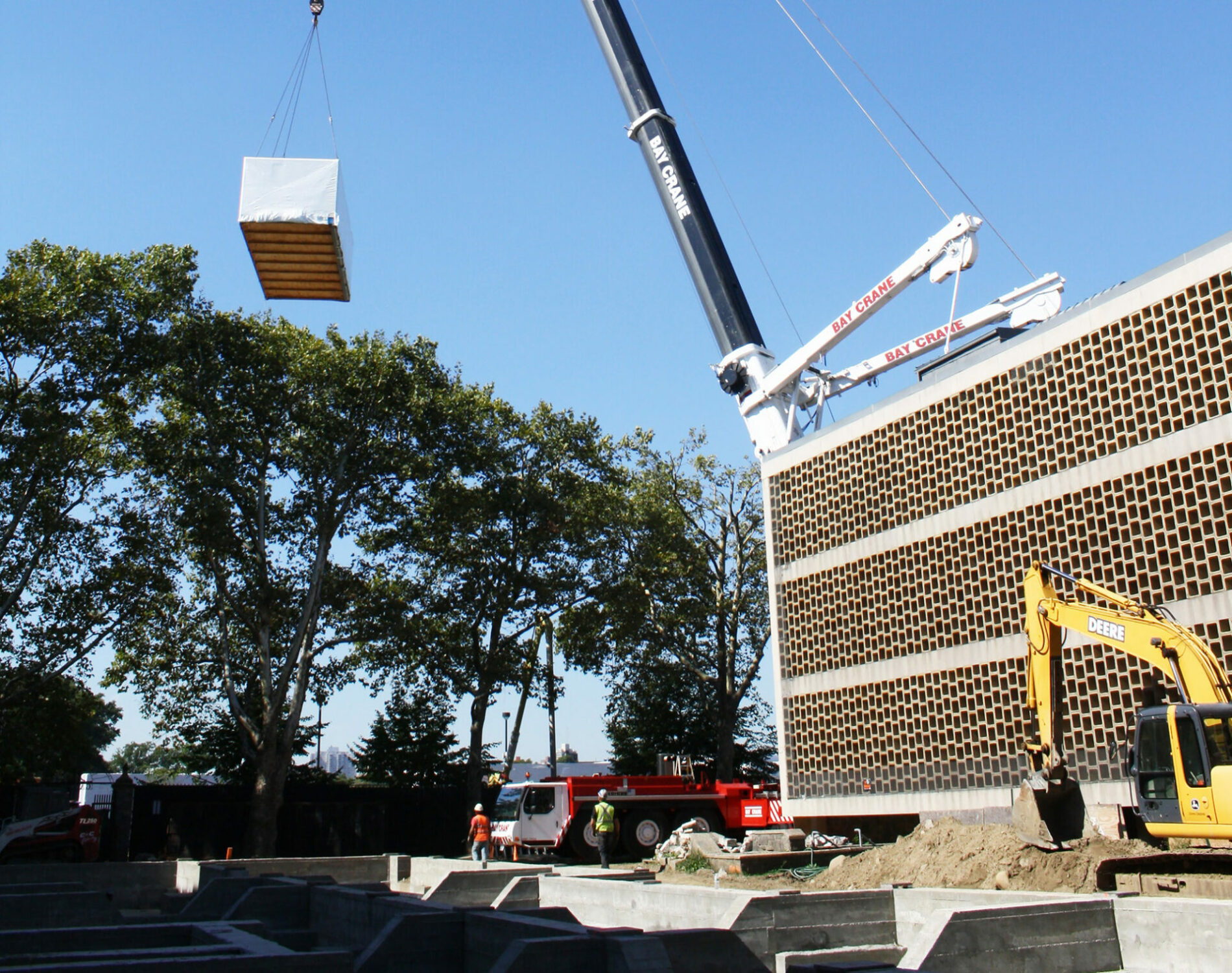
Axis has spent the last three decades working tirelessly in its home State of New York, with further expansion into New England in recent years. The modular division of the company has done a lot of work in higher education, working with universities to build student dormitories. It has also built self storage facilities, large retail supermarkets for major chains, and plenty more. While its portfolio is indeed diverse, the primary focus of the company is healthcare. In fact, Axis has experienced huge success leveraging its modular services to construct everything from emergency rooms, MRI and CT scanning rooms, LINAC buildings, health clinics and even dental offices, predominantly in the bustling metropolis of New York City and New England area.
Axis Construction is one of the few companies that offers modular services for healthcare projects. Due to the specific code requirements necessary to complete a health care-related job, many companies avoid the area entirely. However, this company is different. The complexity of these projects is exciting for the team at Axis and its in-house expertise speaks for itself.
“Collectively between myself and some other individuals on the team, we have over 90 years of industry experience,” says John.
Project highlights for Axis Construction Corporation’s Modular Division include:
City University Of New York, Lehman College Child Care Center
The non-combustible building accentuates modularity by design, with the upper floor offset to cantilever out along the main entrance wall, making it appear stepped. On the east/west walls, classrooms have large sliding doors The non-combustible building accentuates modularity by design, with the upper floor offset to cantilever out along the main entrance wall, making it appear stepped. On the east/west walls, classrooms have large sliding doors opening to a narrow terrace built for planting vegetation. The terrace is screened with handrails and security mesh acting as a trellis for the plants. Vertical polycarbonate tubes provide an aesthetic feature but are also to diffuse light. The trellises and floor to ceiling sliding doors in the classrooms also work as natural clean supply air together with the 20’ x 20’ louvered skylight system in the atrium that can be opened to passively exhaust air. The daycare site was on a very small footprint wedged between two large, active campus buildings, so building off site was a positive consideration in both the projected cost of construction and campus disruption. The construction schedule was reduced by as much as 50% saving the owner significant costs in labor, mobilization, and demobilization as there was limited area to stage materials and work. Onsite activity, disruption and disturbance were minimized which then reduced construction hazards and their associated risks.

Bogner Hall, 3rd Residence Dorm
Bogner Hall, located in Rockville Center, NY, is a 28,000 sq ft, three-story residence hall with a full basement. Designed to house 96 students in double and triple rooms, the building includes modern amenities such as study lounges, private music practice rooms, a large lounge with entertainment facilities, and a fully equipped kitchen. The dormitory is composed of 58 prefabricated modules, assembled using Type II (steel – noncombustible) construction with advanced fire safety and climate control systems.
The modular construction approach significantly reduced the project timeline, cutting the schedule by 50% compared to traditional construction methods. This accelerated completion allowed the college to increase student enrollment a full academic year earlier, resulting in considerable cost savings in labor and logistics. The off-site construction minimized disruption on the active campus, reduced construction hazards, and lowered associated risks. Energy-efficient systems and materials were selected to ensure long-term operational cost savings for the college.
One of the primary challenges was the limited footprint available for the building, situated between two existing residence halls. The modular construction method proved advantageous in this context, as it allowed most of the building to be assembled off-site, reducing the need for on-site material staging and work.
Ultimately, Bogner Hall was a success because of the innovative use of modular construction, which provided precision in fit and finish, reduced on-site disruption, and accelerated the project timeline. The integration of sustainable materials and energy-efficient systems further enhanced its appeal by offering long-term operational savings. The building’s design, which promotes social interaction and modern living, made it a valuable addition to the campus, meeting the needs of both students and the institution.
Beth Israel Deconness Hospital – Plymouth
The BIDH-Plymouth Clinical Decision Observation Unit is the first of its kind in Massachusetts, receiving State Department of Public Health regulatory approval. Designed to reduce operational costs, improved sustainability & enhance the patient experience, it meets all the critical Facilities Guidelines Institute’s guidance for construction. It allows the Emergency Department providers to closely monitor patients for up to 24 hours without admitting to the inpatient unit of the hospital. It is the only certified Center in the area with over 48,000 visits a year. It has 25 private observation rooms, all with the necessary state of the art diagnostic & monitoring equipment to handle 6,700+ visits a year.
It was built completely together inside the plant to ensure precision fit/finish of all features and systems including all med gases & pneumatic Rx delivery system resulting in a shorter site installation time, reduced onsite activity & disruption to the community. Once completed, it was deconstructed & loaded onto transporters, allowing the building to arrive with a very high level of completion, reducing site finish time and minimizing disruption to the campus. Unique floor and roof pan systems were utilized for the center corridor to reduce redundancy while maintaining a high level in finish. Features include fully automatic glass sliding doors, patient, reflective TPO roof, LED lighting, occupancy sensors, RTUs with economizers and fully automated BMS system to reduce energy.
Of course, executing projects like this isn’t always smooth sailing, especially when it comes to navigating the complexities of the healthcare industry. One major issue is the shortage of skilled tradespeople such as electricians, plumbers, carpenters, and welders. This labor shortage also extends to other roles such as project managers and superintendents, particularly as the current workforce is set to retire in the coming years. Despite this, modular construction offers some relief by allowing buildings to be constructed off-site in controlled environments, allowing for the local tradespeople to focus on site work, foundations, utilities and completing the building once installed.
Axis Construction, like many of its peers in the industry, is also dealing with ongoing supply chain issues, resulting in long lead times for essential equipment like HVAC and electrical components, sometimes exceeding 12 months. To mitigate these delays, the company pre-orders long-lead items and actively recruits from colleges and trade schools, investing in young talent to fill entry-level positions and develop future leaders.
Another challenge is the complexity of working in New York City, particularly on large healthcare projects. Navigating city logistics, working with local trade unions, and building codes is difficult, but Axis Construction has built strong relationships with local agencies which enables it to be one of few companies willing to undertake modular healthcare projects in the area. Despite the difficulties, the company leverages its local experience and expertise to successfully complete these challenging projects.
Despite these numerous hurdles, Axis Construction is going strong after three decades thanks to two key values: integrity and client satisfaction. The company prides itself on finishing every job it starts, never walking away from a project or client, even when facing challenges. This unwavering dedication ensures that it can learn from any less successful projects, avoiding repeated mistakes. Prioritizing timely project completion and client satisfaction over its own financial gain has solidified its reputation in the industry.
Remarkably, Axis Construction relies heavily on repeat business, referrals, and word-of-mouth rather than traditional advertising. This strong reputation has been a significant driver of its success. Additionally, Buongiorno also serves as the president of the Modular Building Institute, an international nonprofit industry association. This leadership role enhances Axis Construction’s name recognition and credibility, opening doors to new opportunities, such as potential projects throughout the USA, South America and Europe.
The company boasts a dedicated and experienced team, with many employees having long tenures. This skilled and loyal staff contributes to the company’s stability and consistent performance. Axis Construction values its people and maintains low turnover, which is crucial to its success. Participation in industry organizations and maintaining a high profile within the sector helps Axis Construction stay connected and recognized, fostering growth and new business ventures. This combination of integrity, client focus, reputation, skilled staff, and industry leadership continues to propel Axis Construction Corporation forward in the competitive construction industry.
“This combination of integrity, client focus, reputation, skilled staff, and industry leadership continues to propel Axis Construction Corporation forward in the competitive construction industry.”
Looking ahead, the company is poised for significant growth —especially within its modular division. Recognizing the rising interest and demand in the modular construction industry, the company is expanding this division considerably. It has recently opened a new office in the Boston/New England area, a hot market where it is rapidly increasing its workload. To support this growth, Axis is actively hiring, including a dedicated business development professional to focus on opportunities in New England.
The company’s modular division, which previously contributed about 10% of annual revenue, has seen remarkable growth. In the past few years, this contribution has surged to over 20% and is projected to reach 30% next year. This expansion underscores the division’s success and Axis’s commitment to scaling its operations.
Axis Construction’s future plans, however, remain deeply rooted in its family-oriented ethos. The owner, with no intention of selling the company, is focused on succession planning, and ensuring the company’s longevity. This includes mentoring and training younger employees to take on leadership roles. The company’s overarching goals are longevity, mentorship, and the successful transfer of knowledge to the next generation. By fostering a culture of mentorship and strategic hiring, Axis Construction is not only mitigating the loss of industry veterans but also ensuring its continued success and stability for years to come.
Think Axis Construction Corporation could support your modular needs? Reach out to Either John via email at [email protected] or Brent Doucette at [email protected].