In construction, it is often said that the best solutions are the simplest—the most direct and straightforward. According to Vice President Greg Arvai, Ontario based IECS is in the business of simple, specifically “innovative infrastructure solutions that save time”. It is evident, in conversation with Arvai, that clarity and honesty have been, and continue to be, key to the development of the company’s concrete products and working relationships. Integrity in construction involves constantly striving to be more efficient, not only in immediate terms such as speed, but in the long-term best interests of the local community and environment.
“It’s kind of just the way we operate,” Arvai says without fanfare. “It’s just our business model, which is beneficial for everyone.” This model is based on two core product lines: custom precast concrete structures and Cable Concrete, a trademarked articulated concrete block mat system. Up until now, the precast service has only been available in the Ontario region, but this will soon change. Meanwhile, Cable Concrete has been internationally exported for years as a versatile solution for erosion control. The two sides of the business are distinct but interrelated, as Arvai explains over the course of our conversation.
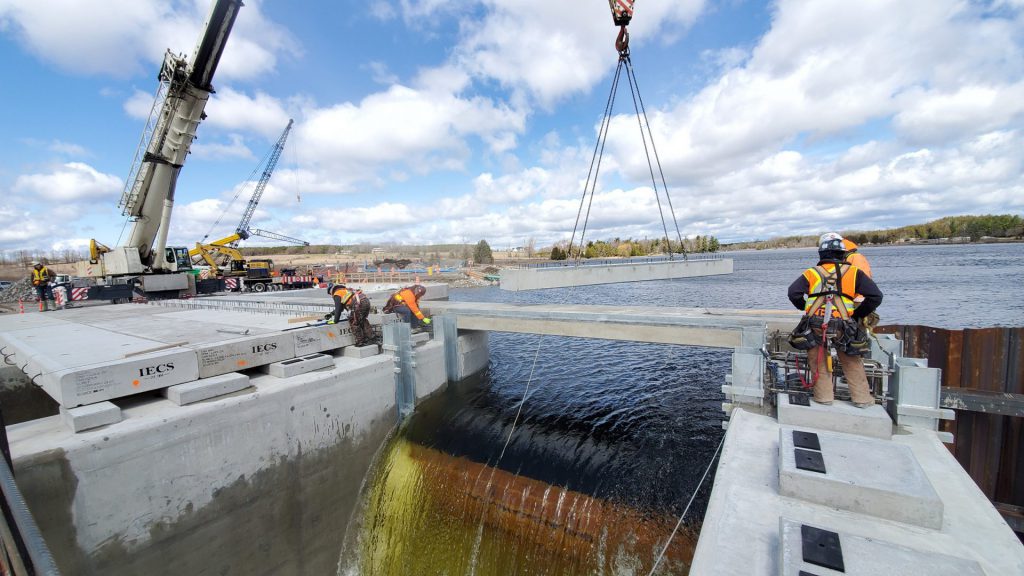
Precast concrete was the starting point of the company founded in 1984 by Arvai’s father, Louis. Originally pouring concrete for domestic driveways and sidewalks in Ontario, he and his partners then started precasting patio stones. A series of progressions and modifications to the precast product line resulted in Cable Concrete, a turning point for the growing business. An ACB mat system connected by cables, it forms flexibly to the ground’s surface and can be easily cut to fit irregular shaped areas. Initially only available in one block size, it evolved through lab studies and testing into the fully engineered offering it is today, customizable according to the stability required.
Looking at online images and videos of Cable Concrete being installed and in situ, one is struck by the appealing simplicity of its appearance. Rows of neat blocks adhere easily to the undulations of the landscape, belying the sophisticated engineering that went into their design. The mats can be completely vegetated, ultimately becoming invisible. This solution is also safe for pedestrians and animals because the blocks cannot be dislodged or vandalized like loose rocks. It is also a more sustainable option, compared to riprap, which is a non-renewable resource and one that is an expensive import to places where it is not native or readily available.
“Ultimately, we’re just coming in as an engineered solution and offering support.”
When Cable Concrete is imported as an engineering solution, the actual blocks will be made locally, with local materials and local workers. The steel molds are manufactured by IECS in Canada, from where they can be shipped to any location across the globe. This mode of production is a factor in the company’s capacity to turn out large-scale erosion control and pipeline protection projects in far flung locations, while maintaining a lean staff. The economic and other benefits are not just one-sided though. Job creation, along with a sense of real involvement in and ownership of projects is a positive legacy to leave with the communities who will live with these structures. Local teams will be supported by training and project management teams from IECS who will oversee the project. As Arvai describes it: “Ultimately, we’re just coming in as an engineered solution and offering support. And other than that, it should be looked at as a local product and a local success story.”
As Cable Concrete took off in the late 1980s, the precast product line was also growing and diversifying. It began with headwalls in residential areas. Louis and his then partner Charlie kept seeing them in the plans of projects for which they’d been brought in to install concrete mats. The two wondered if they could cast them and after some experimentation, IECS was the first to market with a precast headwall. From there they diversified further, on to larger box culverts, box manholes and bridge elements, drawn to anything unique and challenging, a factor in their move towards heavy civil structure projects. One of very few companies willing to take on some particularly difficult challenges, IECS still offers a fair price. As Arvai tells it: “Our norm is these unique projects. We can offer the market custom structures with a non-custom price tag and offer competitive solutions.”
These bespoke solutions also have the additional benefit of streamlining the process for contractors considerably. Specializing in large scale structures, IECS offers segmental precast alternatives that save contractors time and money, while also cutting down on other processes such as shoring, dewatering, and bypass pumping. Items traditionally formed and poured on site can take 4-8 weeks to do so, whereas ones manufactured off site at the IECS facility can be installed in a matter of days. There are also improvements in quality, when the pouring is done in a completely controlled environment, within an enclosed facility. Quality is improved and weather variables do not need to be accounted for, making scheduling easier. Contractors also do not need to sub out as much work; they can use their own team and their own equipment to lift the large precast structure from the trailer and move it into place.
“We want to be fair. We want to offer good products. We will continue to grow our product line.”
On the subject of sustainability, Arvai explains that it is built into the company’s business model, as shipping and unsustainable resources are avoided as much as possible. The concrete used today is also more environmentally friendly than the type used previously and the production facility is constantly upgraded with the latest energy efficient tools and materials. A newly acquired rebar bending and cutting machine promises to reduce energy consumption and steel waste by 20%. On the subject of ethics, Arvai is frank: “We want to be fair. We want to offer good products. We will continue to grow our product line. We will continue to grow the solutions we offer our industry. We’re not going anywhere. We’re very excited about the future.”
There’s a lot to be excited about. In 2021 the team will commence work on the biggest project it has ever been involved in to date: the Davenport Diamond Grade Separation Project, owned by Metrolinx. The bridge will be constructed in collaboration with design engineer IBT and contractor Graham Construction. Work is also underway with multiple contractors on five of the new dam projects on the Trent-Severn canal, for Parks Canada. IECS will build the bridge decks for these.
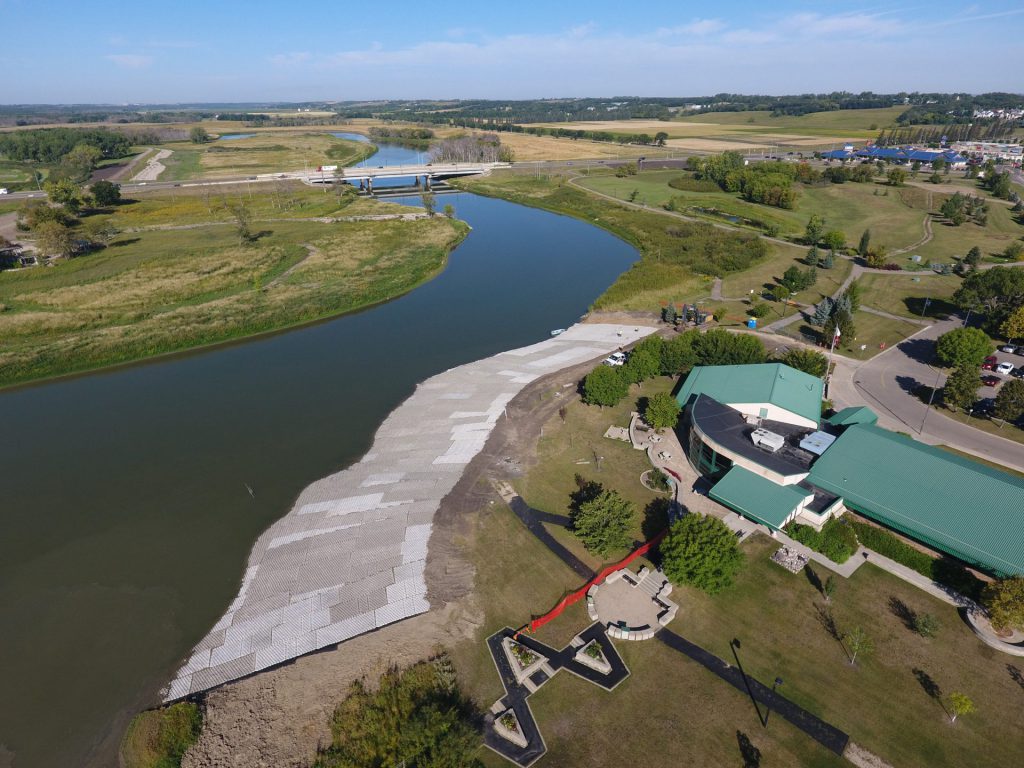
At the time of writing, the potential for geographical expansion is growing. Cable Concrete is in the approval process for the list of products officially endorsed by the Ministry of Public Works in Chile. This approval would create opportunity and diversification, by opening doors into previously uptapped markets. Once this approval happens, the product can be specified for use on any federal or government funded projects, and will naturally also come into the radar of private sector contractors. As Chile strives to be a leader in innovation in the region, Arvai believes that this will also open the door for business in surrounding countries in South America.
Recent big investments in facilities will support these and other projects. The Ontario manufacturing shop was recently extended with a 25,000 square feet area specifically for custom precast products. It is in the location that the Davenport Diamond Bridge will be manufactured. The facility boasts a 70 ton overhead crane indoors, along with an 80 ton rubber tire gantry crane in the yard. Land has also been purchased in Saskatchewan, with plans to establish a new fabrication shop and headquarters in Humboldt, to offer customers in the west of Canada a greater range of precast products beyond Cable Concrete.
“He speaks proudly of the current staff roster, which he describes as bright, open-minded, and a great mixture of young and old.”
In contrast to many, the IECS experience of the pandemic was not one of surviving but thriving. 2020 was in fact the company’s most successful year to date. Lots of existing contracts were deemed essential by the government, allowing work to continue, albeit with additional safety measures. There were no virus cases among workers at the manufacturing facility or those based in the office. Despite, or perhaps because of, the surrounding uncertainty that unfolded as the pandemic raged on, the 110-strong team became closer. Arvai attributes this to a positive work culture. Despite the scope of its endeavours and ambition, there is still something refreshingly down-to-earth about this family-run business, with its base in a small rural area. For Arvai and his father, maintaining a “big family” feeling is important. He speaks proudly of the current staff roster, which he describes as bright, open-minded, and a great mixture of young and old.
Optimism around the work is another key value. “We have a core belief that we can solve any problem,” he says, and this clearly extends beyond engineering challenges to interpersonal dynamics and international collaborations: “We want people to know that there is no country or city that we won’t visit. If there’s an opportunity where we can come in and offer a solution, then we’re willing to make the journey and establish the relationship and the trust that is needed to do business, and build that solid relationship with new people. We love meeting new people.”